Foundations represent the major infrastructure of any offshore wind farm: supporting the wind turbines in a very challenging environment, foundations often account for a large portion of the total equipment cost. Selecting the right kind of foundations is hence key for the economic viability of any project.
Only a few locations can be selected for offshore wind farms, with limitations due to the maximum depth of the seabed (greater depth means higher cost) and the distance to coast (greater the distance from the coastline, greater the size and the power of the turbines that can be deployed but also, generally, greater the depth). The trend is, however, to place these installations further from the coastline than ever before.
Different foundation technologies can be deployed, such as Gravity-Base Structures (GBS), Monopiles, Tripods, Jackets and, more recently, Floating. Among these, monopiles stand out for both frequency and range of use at different seabed depth. Due to their simplicity and adaptability, Monopiles are currently being selected in more than 60% offshore wind installations.
Monopile design has constantly being improved to accommodate more and more demanding wind-farms: diameter, thickness and length have steadily increased for supporting higher and heavier turbines installed at greater depths. As an example, Monopiles for a 6-7 MW turbine are typically 100m long, with bottom sections diameter and thickness of 9m and 100mm respectively for a total weight often exceeding 1500 ton. However, offshore wind turbines capacity will certainly increase, with 12-14 MW turbines already being tested: the required so-called XXL Monopiles are expected to weigh up to 3000 tons reaching 12-14m diameter and 120-140mm thickness at their bottom sections.
The manufacturing challenges
Offshore foundations are large plates rolled into cans and cones, assembled and welded into large structures reaching up to 120m in length. With thicknesses approaching 140mm at 12-14m diameter, it becomes critical to minimize the amount of circumferential welding, hence minimizing the number of workpieces needed to achieve the desired total structure length (leading to select larger and larger plates, up to 4.5m in width).
Fabricators are hence required to overcome two main manufacturing challenges: managing increasing ratio between diameter and thickness (high ratio leading to workpiece instability and deformations compromising the rolling accuracy) and handling highly unbalanced tapered plates required for large diameter conical sections with angle up to 14° (used to transition from bottom to top sections of the Monopiles).
All the above makes off-shore foundations rolling operations very challenging indeed!
Stay ahead of the Market with DAVI!
High performance and reliable rolling solutions must then be provided, with serial production requiring high accuracy and repeatability while guaranteeing operators safety and minimized downtimes.
DAVI has been leading the market since 2007, when a dedicated Wind Energy Division was created, through cutting-edge technologies developed working alongside the main players in the Sector. Dedicated feeding and handling accessories are continuously being updated to provide fabricators with the most advanced equipment allowing them to gain a competitive edge in a dynamic environment where increasingly challenging workpieces have to be manufactured every year.
DAVI market dominance is confirmed by more than 300 installations operating in the Wind Energy Industry for a rolling machines Market share close to 60%. Don’t miss out, stay ahead with DAVI!
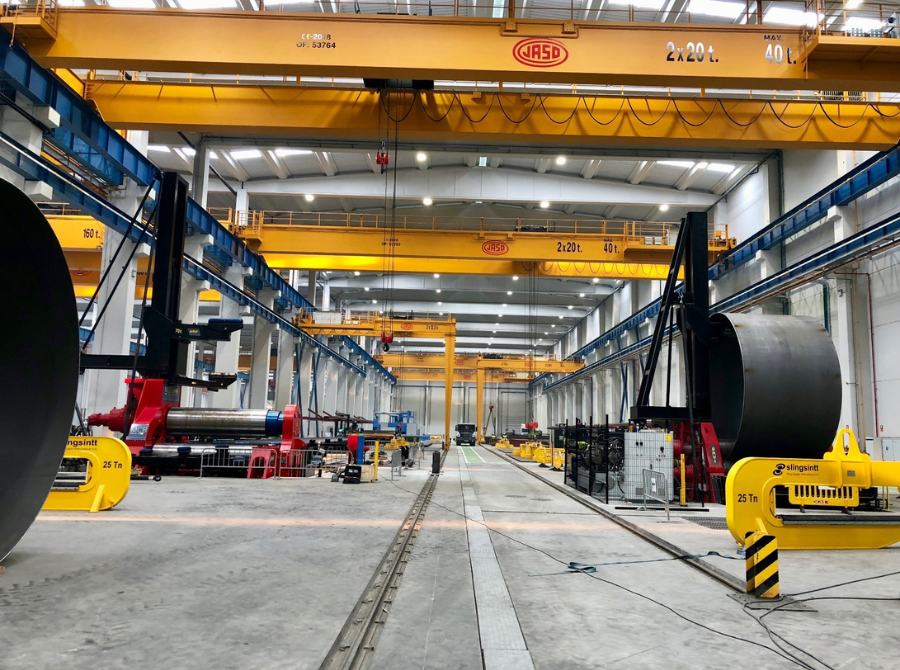