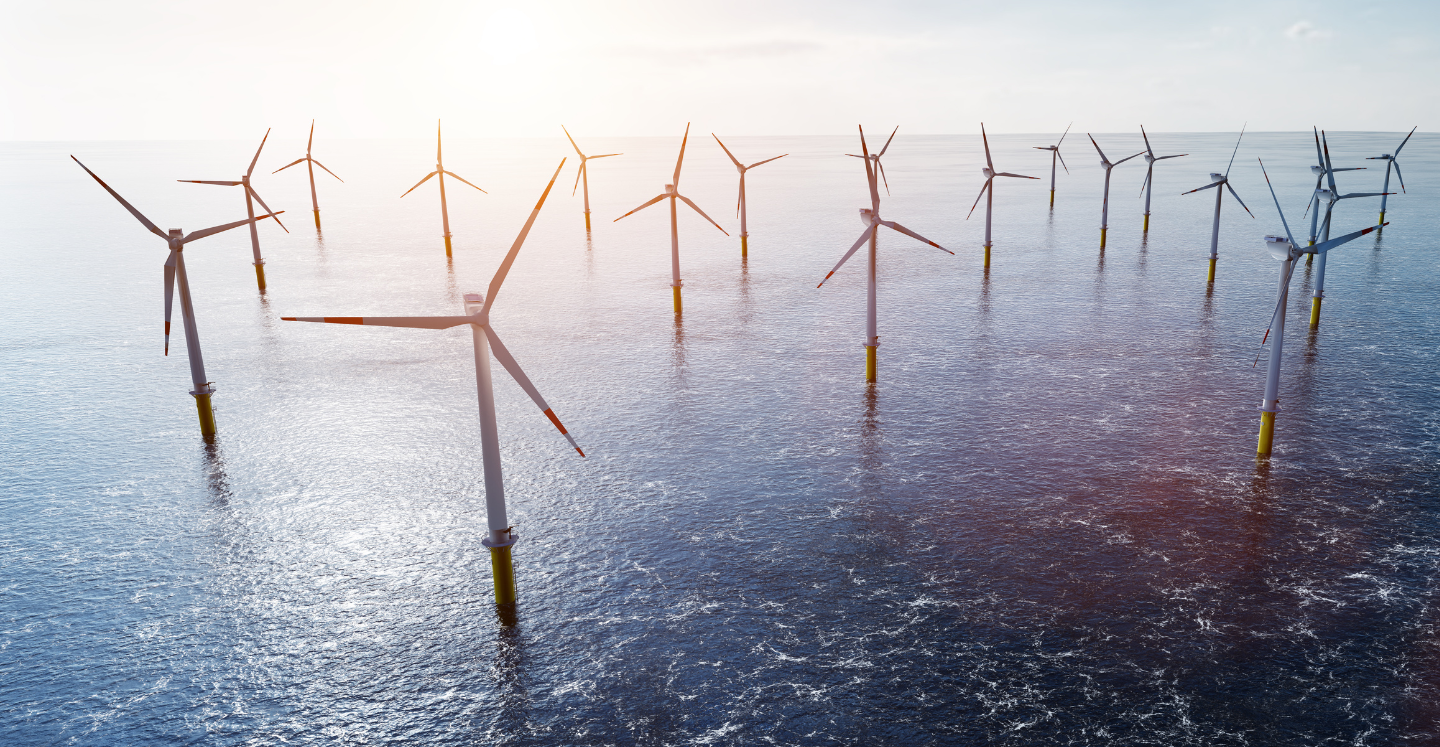
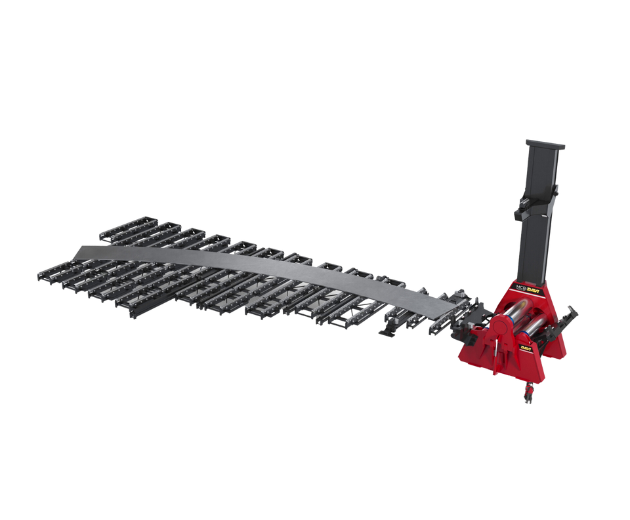
Davi numbers in Wind Energy
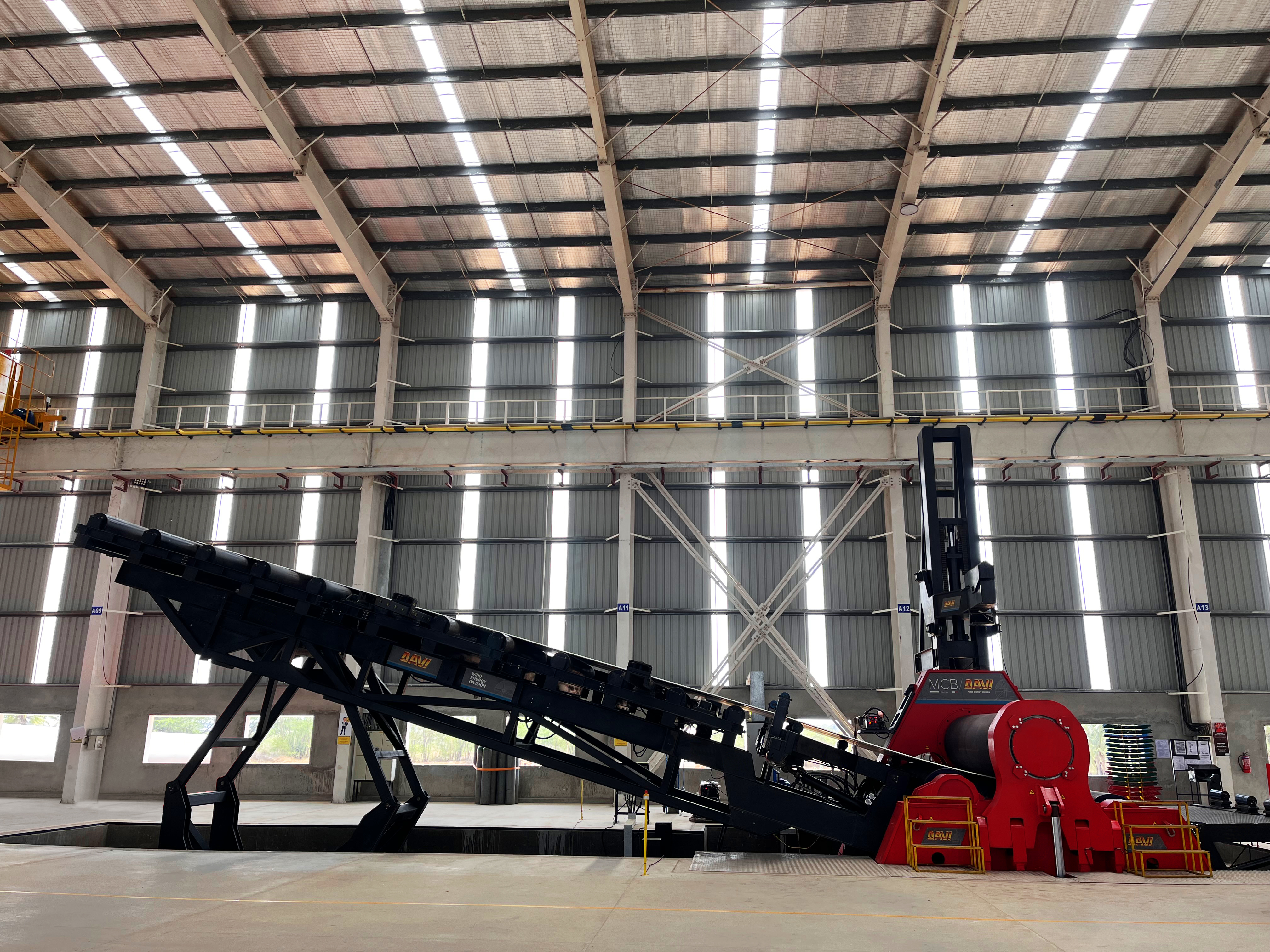
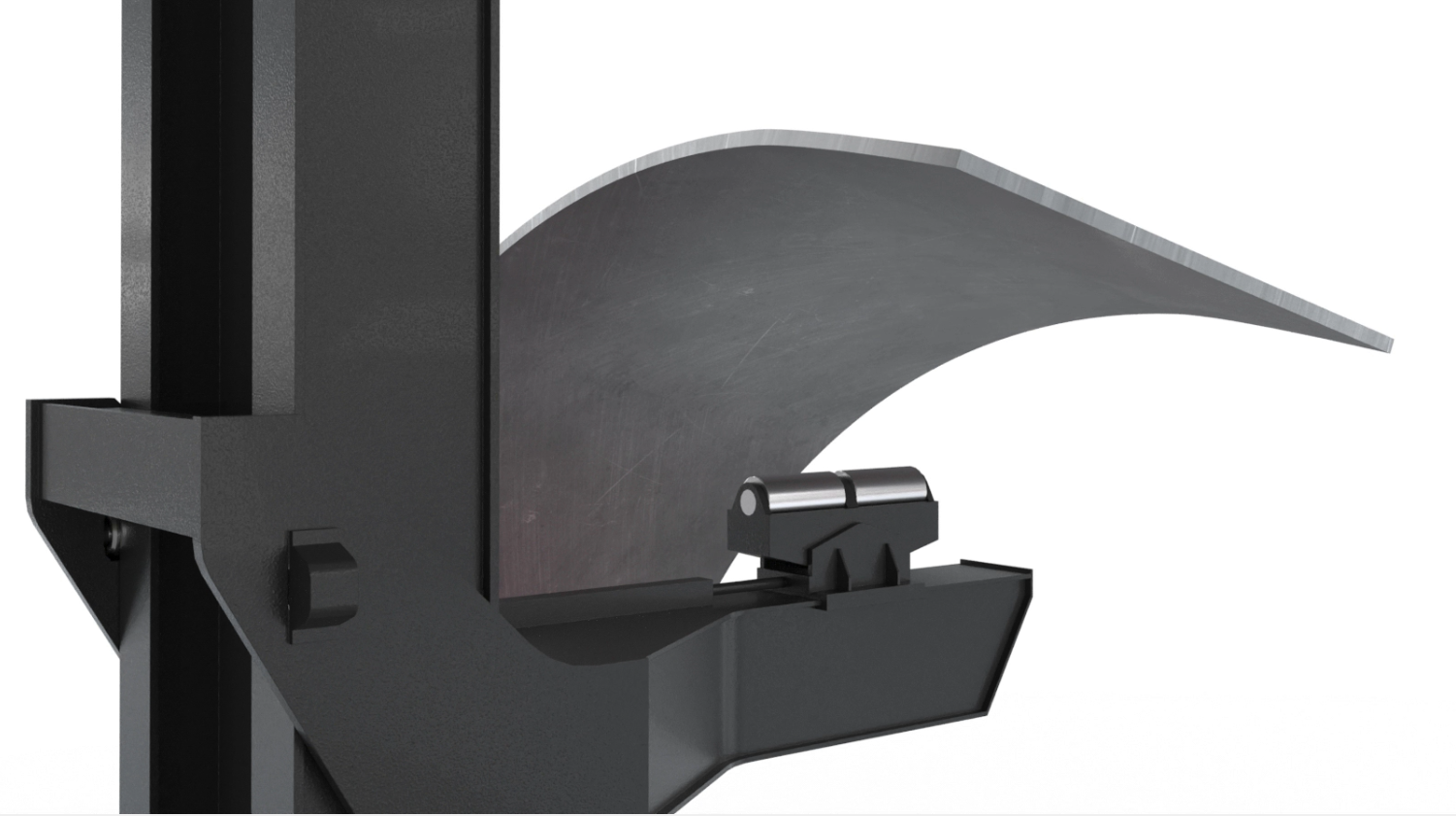
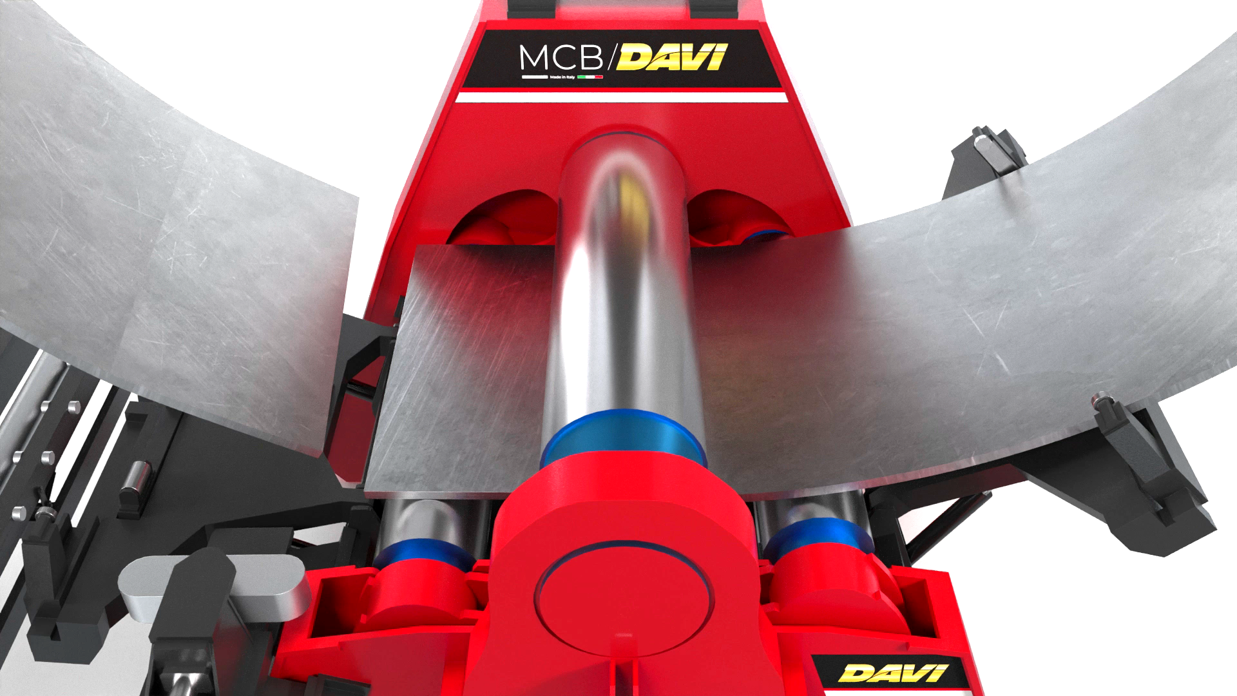
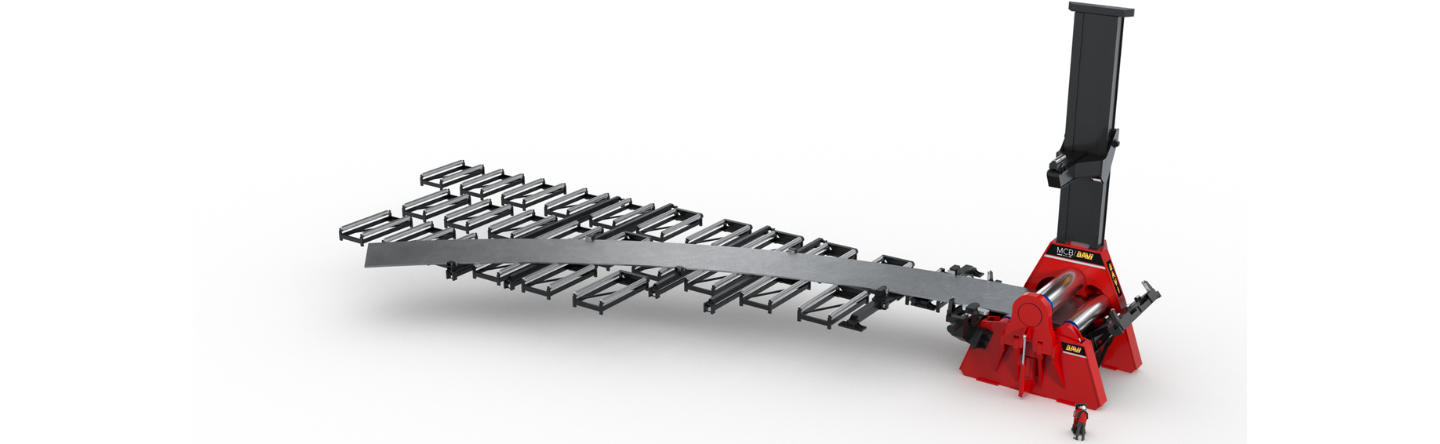
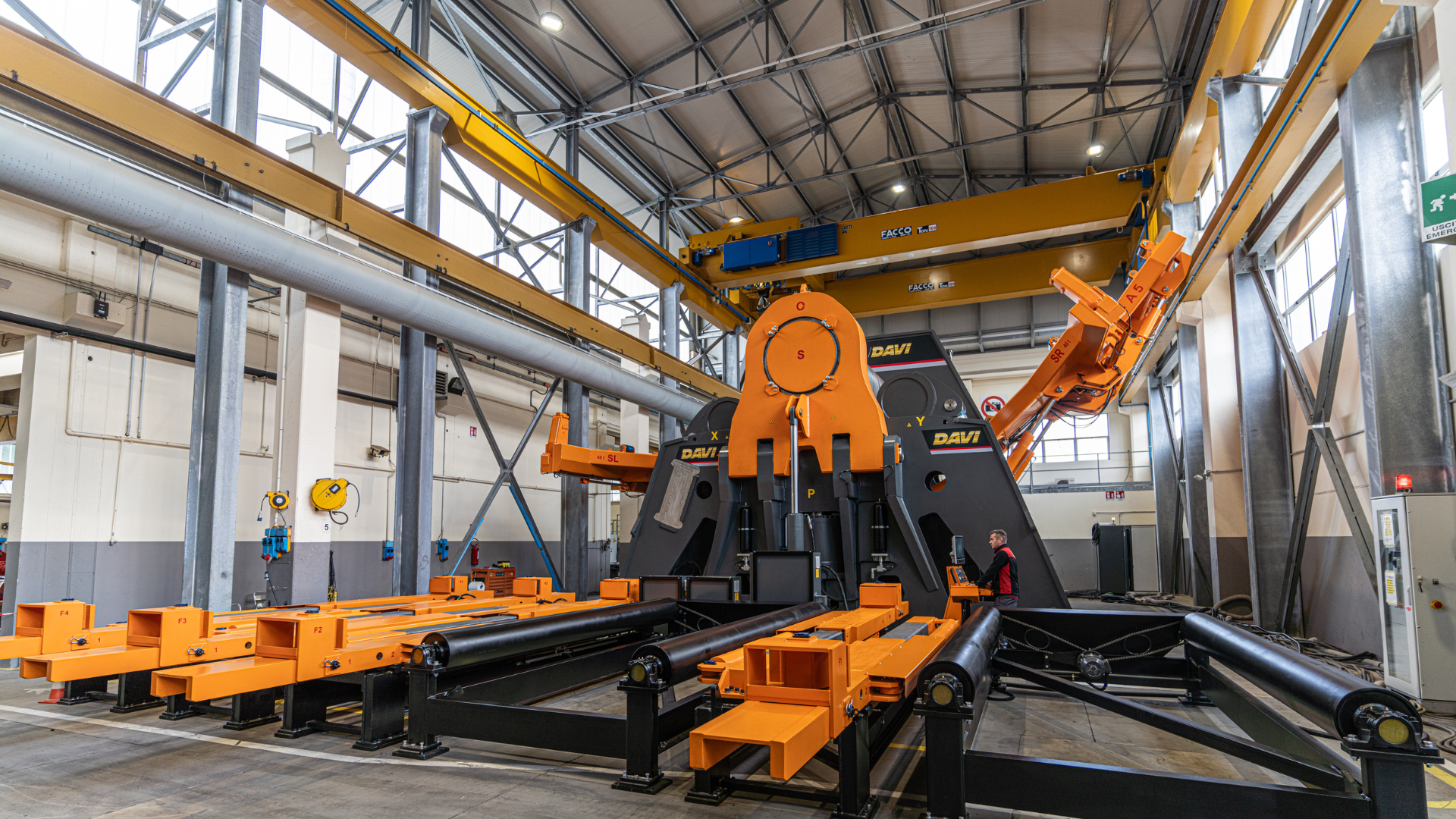
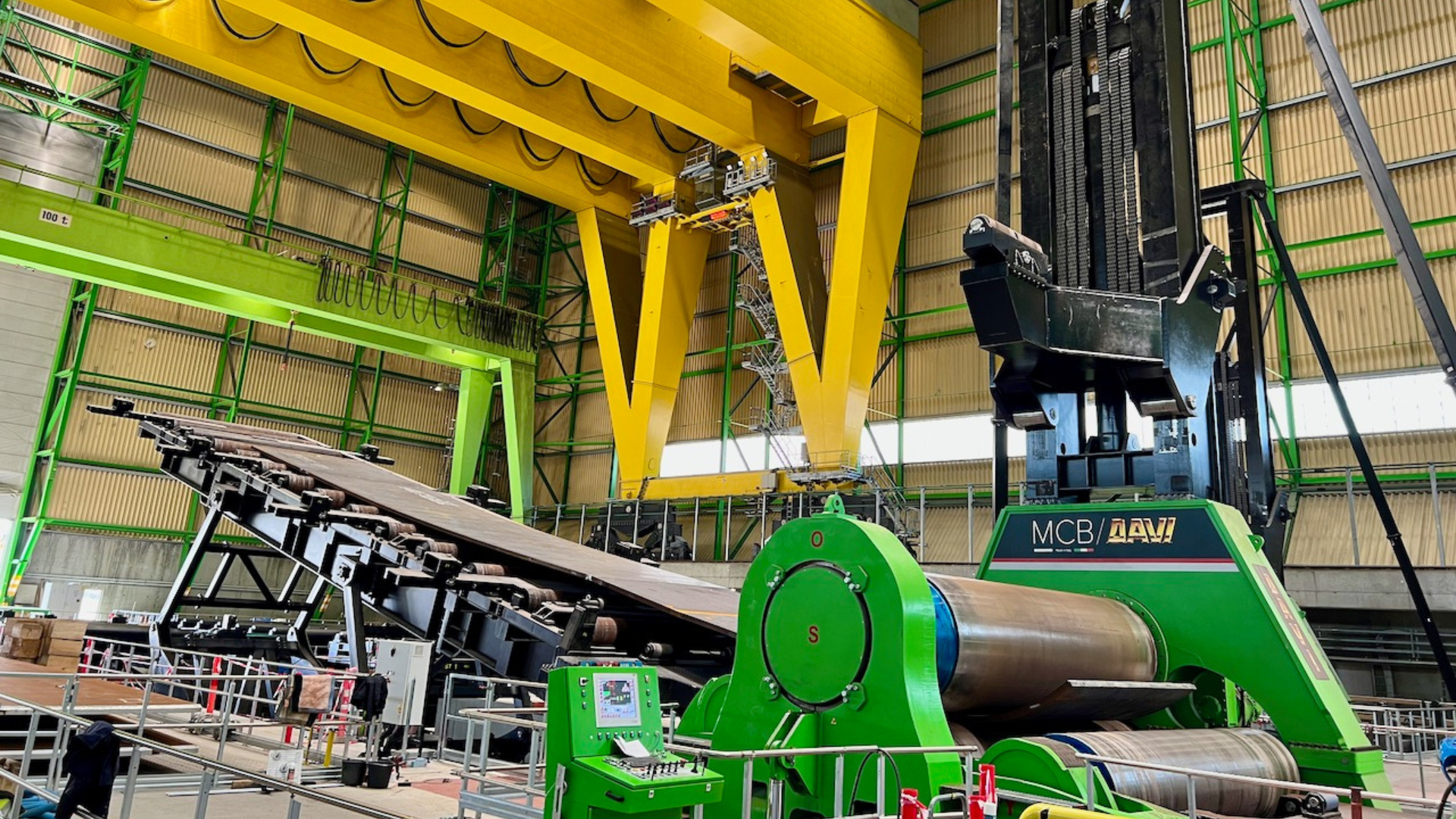
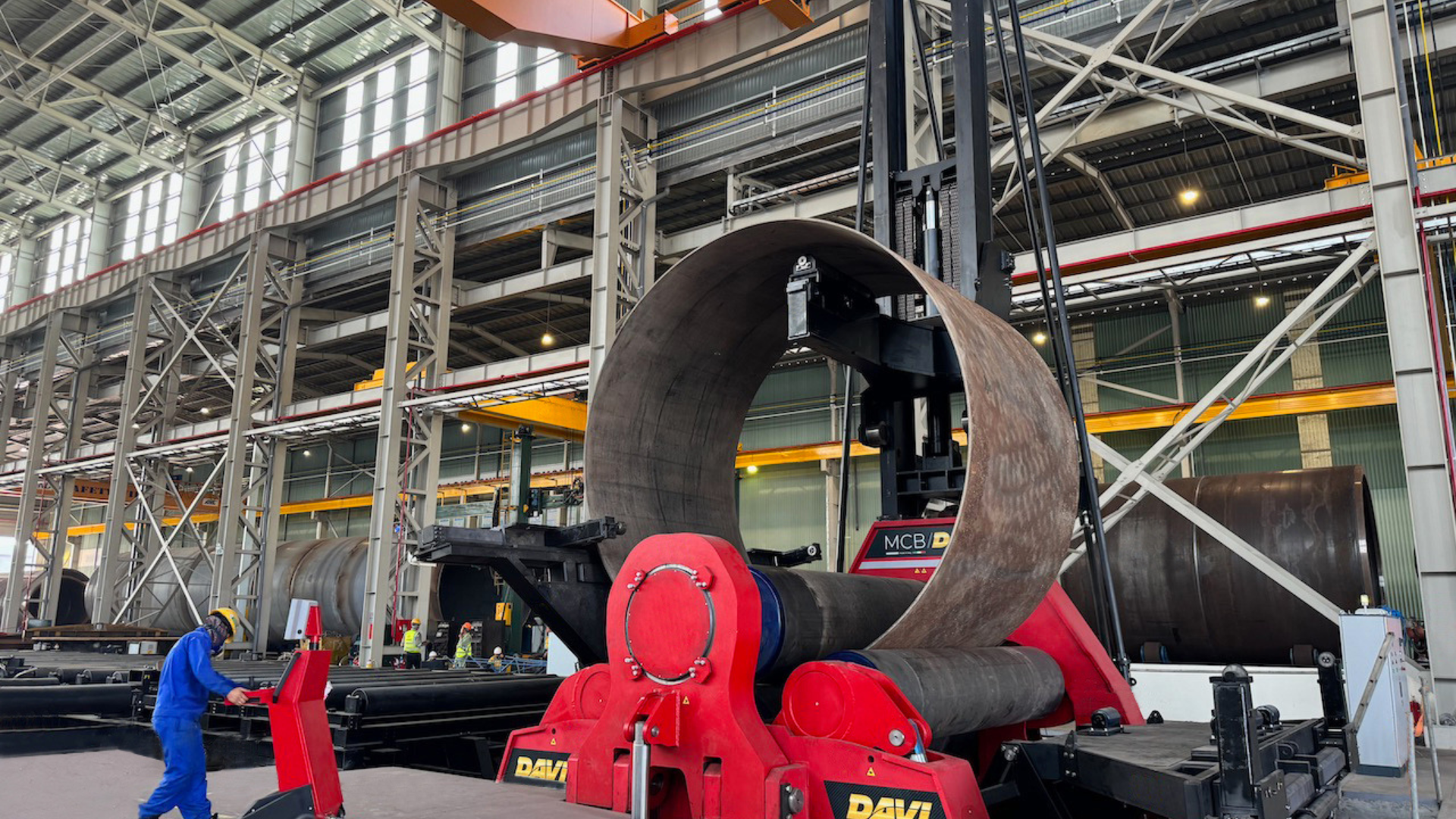
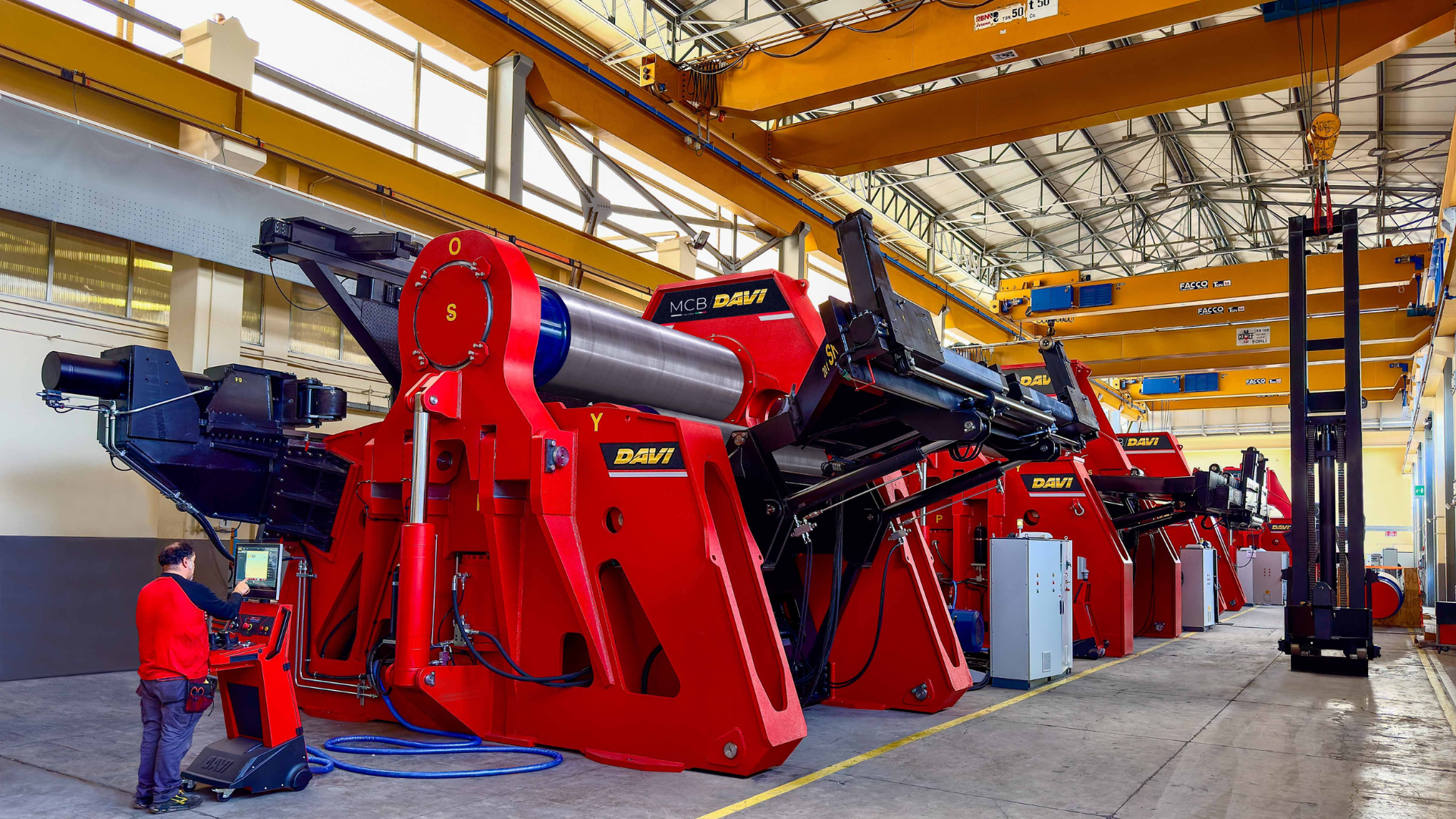

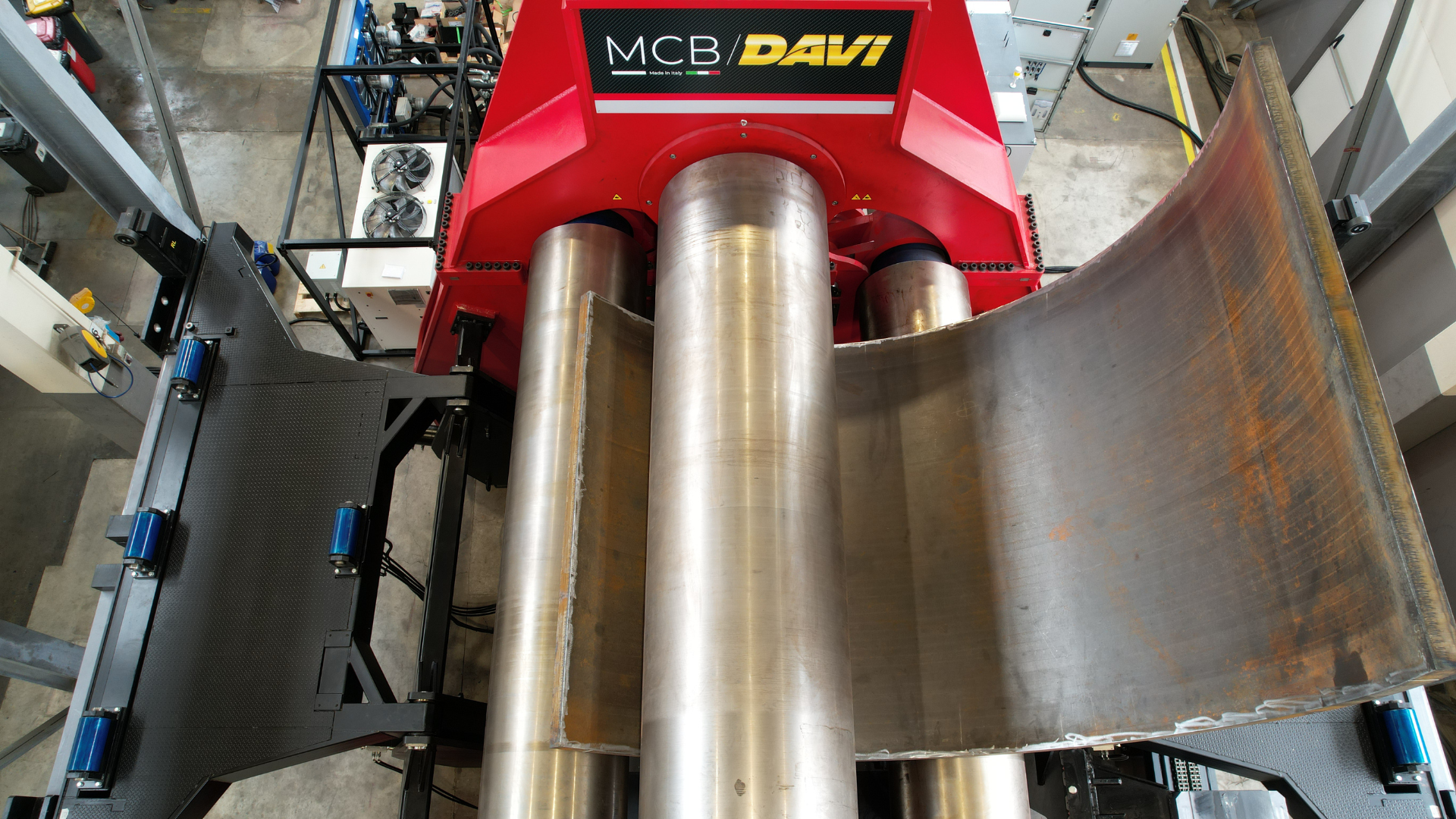
Monopiles
Monopiles are foundation structures that typically have a diameter ranging from 7 to 15 metres (23’ to 50’); they are made of steel, using plate up to 4 or 4,5 metres (13’ or 15’) width and thicknesses varying between 50 and 170 millimetres (2" to 7"). Monopiles sections are cylindrical and conical in shape. Their maximum length can reach between 80 and 120 metres (262’ and 394’); they weigh between 3,000 and 4,000 tons. Monopiles are designed to be driven into the seabed and provide support for wind turbine towers. They are used in water depths ranging from 50 to 60 metres (164’ to 196’). The angle of conicity, which is the tapering of the conical part of the structure, varies between 10 and 16 degrees.
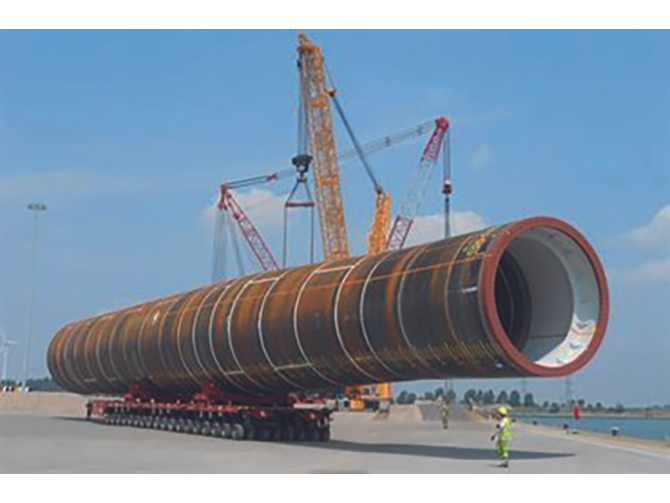
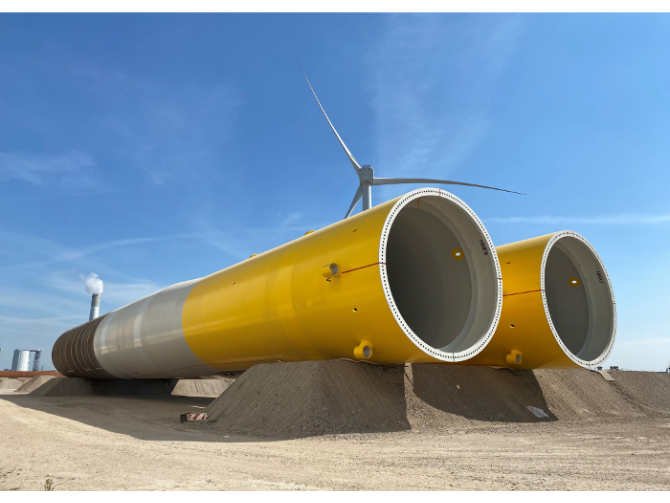
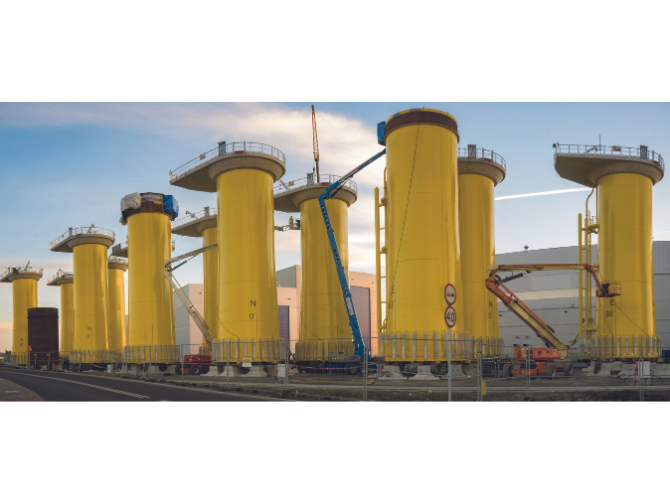
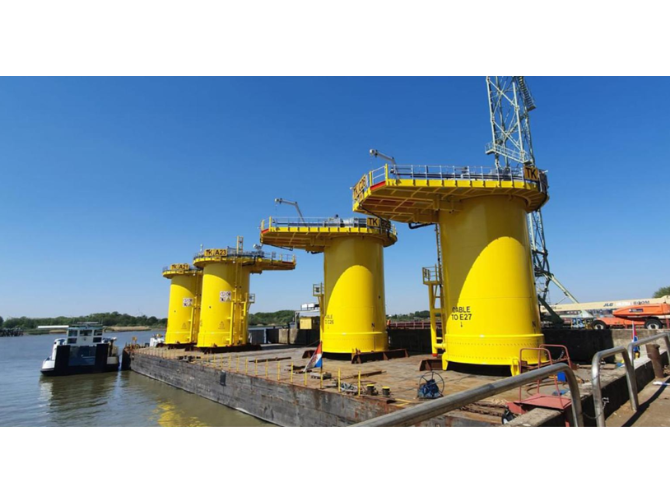
Transition Pieces
Transition pieces serve as a crucial connection between the monopile foundation and the wind turbine tower. They have a diameter that typically falls in the range of 6 to 12 metres (20’ to 40’), with a maximum thickness of 150 to 170 millimetres (6" to 7"). Transition pieces are designed to accommodate the transition from the wider monopile to the narrower tower. They are made of plate up to 4 or 4.5 metres (13’ to 15’) wide; in general they are cylindrical with flanges but sometimes conical with an angular configuration of 10 to 12 degrees. The maximum length of a transition piece is about 32 metres (105’), and they typically weigh between 1,500 and 2,000 tons. These pieces play a vital role in ensuring the stability and integrity of the entire offshore wind turbine structure.
Tripods
Tripods are specialized foundation structures used particularly in water depths ranging from 45 to 50 meters (148’ to 164’). They have a unique three-legged design, which is why they are called tripods. The diameter of each leg can vary from 3 to 10 meters (10’ to 33’), and the steel thickness can be as thick as 120 millimeters (5”). The width of the tripod's steel plates is typically 4 to 4.5 meters (13’ to 15’), and they can weigh up to 4,000 tons. Tripods are designed to provide stable support for wind turbines in deeper waters. Their triangular configuration helps distribute the load evenly and secure the turbine tower in place. Tripods are an innovative solution for harnessing wind energy in challenging offshore environments.
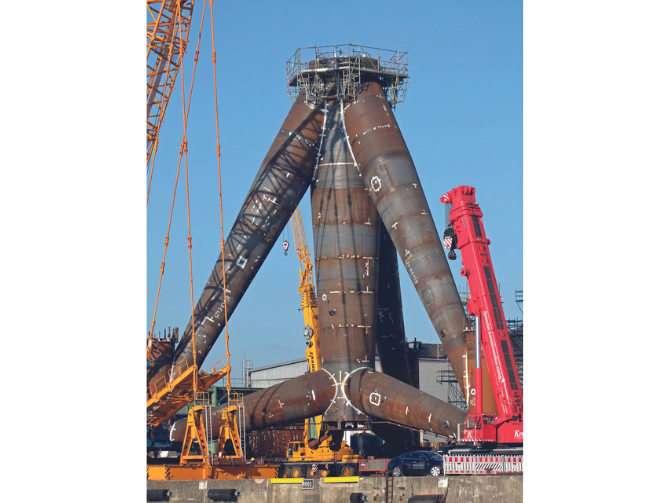
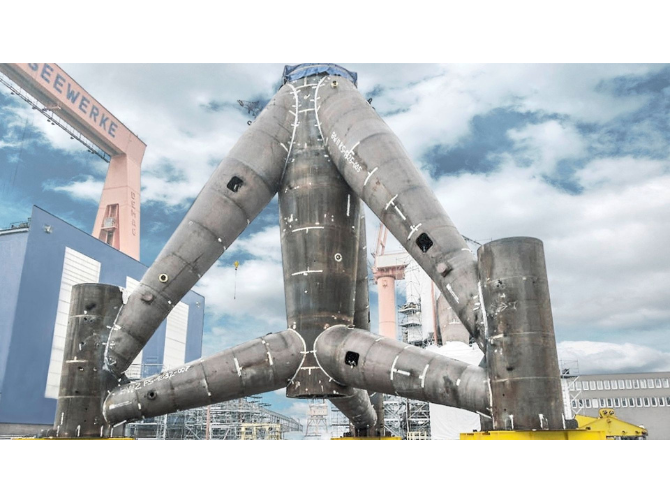
DAVI SOLUTIONS FOR MONOPILE FOUNDATIONS
When it comes to the construction of robust and reliable monopile foundations for offshore wind turbines, Davi offers a comprehensive suite of cutting-edge solutions that set the industry standard.
Machine Expertise
Davi's core offering includes state-of-the-art machinery specially designed for monopile production. Our machines are equipped with a range of accessories, including vertical and lateral positioning capabilities, which allow for precise and efficient manufacturing. These accessories ensure that the fabrication process is not only highly accurate but also adaptable to the uniquerequirements of each product.
Circumference Measurement
Davi incorporates cutting-edge technology for the shell's circumference measurement. This specialized measurement tool provides accurate data on the shell's circumference, a vital parameter for an accurate fitting in the following Monopile growing line. Ensuring the monopile structural performance and the utmost safety and reliability in offshore wind installations.
Computer Numerical Control (CNC)
The heart of our monopile production process lies in our advanced CNC technology. Through CNC, we can meticulously control and manage the entire manufacturing process. This results in superior reliability, unparalleled quality, optimized output performance, and substantial energy savings. Our CNC systems are at the forefront of automation and precision, ensuring that every monopile meets the highest industry standards.
Automatic Radius Measurement
Davi's solutions include automatic radius measurement, a critical feature that guarantees the exact dimensions required for proper fit and stability. This auto-mated process not only enhances the precision of the monopiles produced with DAVI machines but also expedites production, reducing project timelines and costs. The measurement operation is safer and more accurate compared to standard manual measurement methods with templates.
In conclusion, Davi's solutions for monopile foundations are characterized by innovation, precision, and efficiency. Our machinery, coupled with advanced CNC technology and automatic measurement systems, guarantees that every monopile produced meets the highest industry standards for reliability, quality, and energy efficiency.
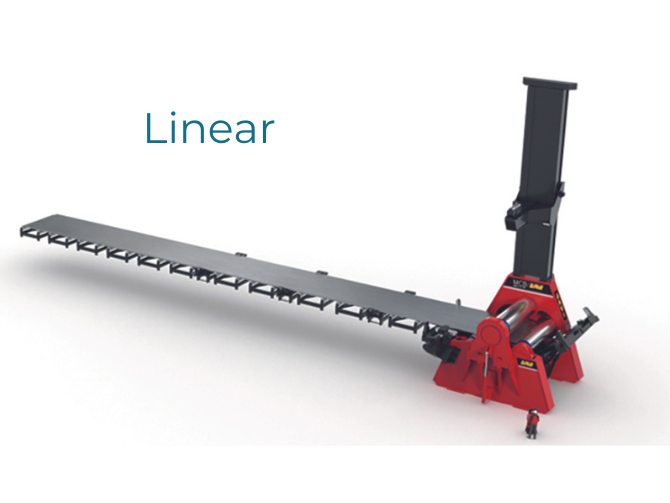
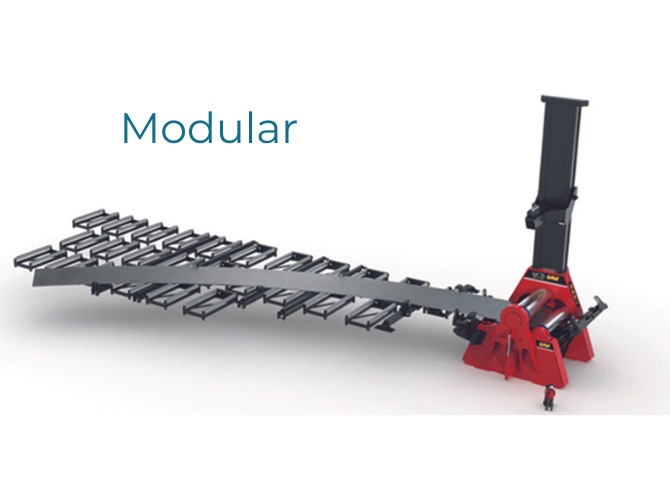
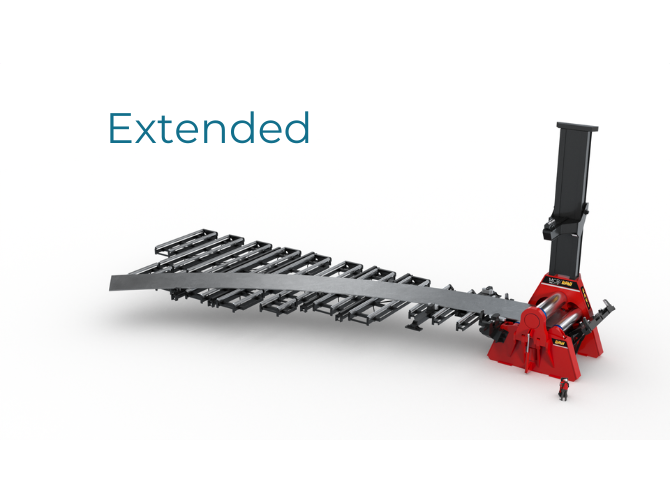
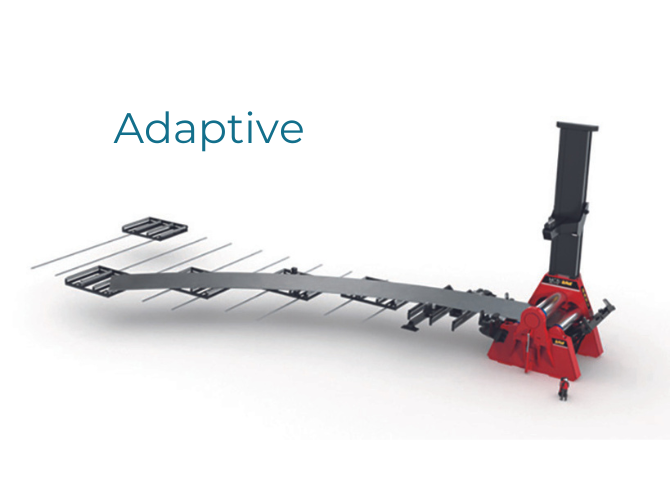
Feeding Systems
Linear
Ideal to intensively produce cylindrical cans. In case of cones, the plate must be partially supported by cranes.
Modular
To intensively produce cylindrical cans. Cones are also possible with repetitive plate adjustments. The plate must be loaded and positioned by cranes; only a fine tuning alignment is possible with pushers. In case of cone forming, the intermittent and time consuming plate rotation is made through pushers.
Extended
To intensively produce cylindrical cans and cones. The plate can be loaded on conveyor in any position and the manipulator system automatically operates the plate positioning and alignment. In case of cone forming, the plate rotation is made continuously and automatically with the SMART LINE feeding system; or intermittently with time consuming repositioning through pushers.
Adaptive
To intensively produce cylindrical cans and cones. The plate must be loaded and positioned by cranes; only a fine tuning alignment is possible with pushers. In case of cone forming, the plate rotation is made continuously and automatically with the SMART LINE feeding system; or intermittently with time consuming repositioning through pushers.
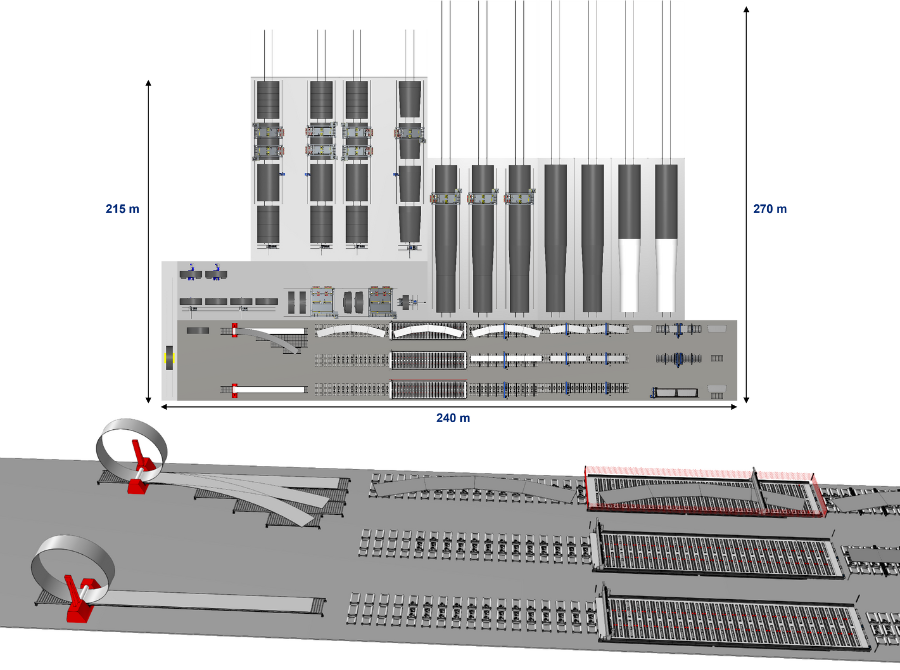
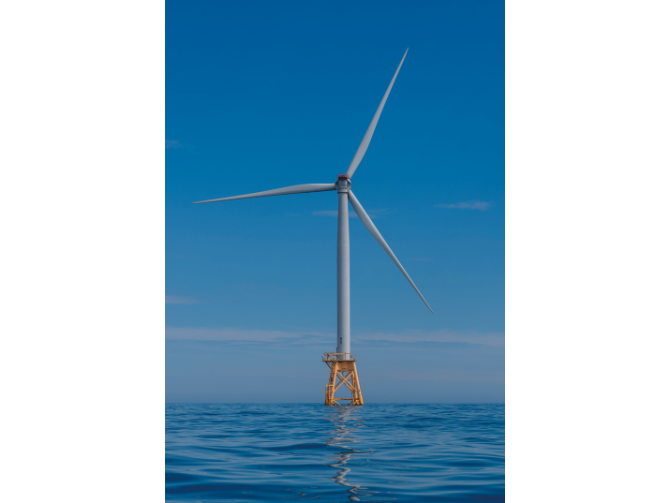
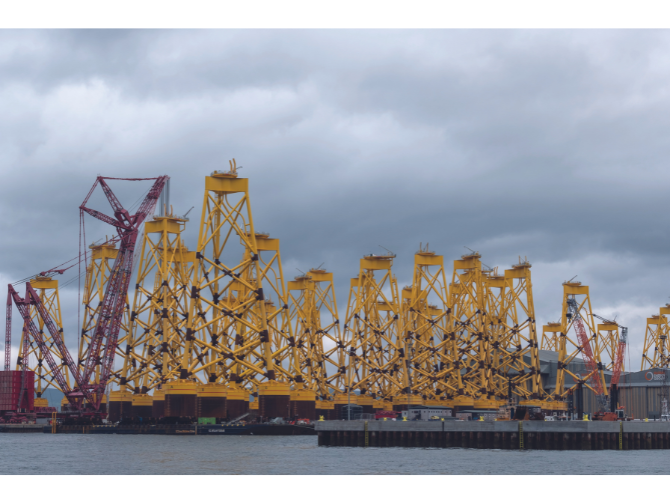
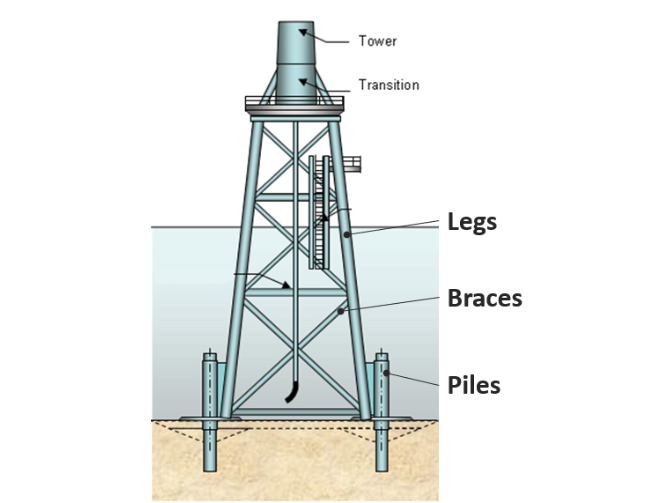
Jacket Foundations
Transition Piece (TP)
At the top of the jacket foundation, you'll find the Transition Piece (TP), which acts as the connection point between the structure and the tower. With diameters ranging from 6 to 10 meters (20’ to 33’) and thicknesses of up to 100-120 millimeters (4”-5”), the TP plays a critical role in anchoring the entire tower securely.
Legs
The sturdy legs of a jacket foundation are the primary load-bearing components. These robust structural elements come in diameters ranging from 1000 to 2500 millimeters (40” to 100”), with thicknesses varying from 50 to 120 millimeters (2” to 5”). The legs provide the necessary strength and stability to support the weight of the offshore structure.
Braces
Braces serve as diagonal supports within the jacket foundation structure. With diameters ranging from 600 to 1200 millimeters (24” to 48”) and thicknesses of 35 to 40 millimeters (1”3/8 to 1”5/8), they play a crucial role in distributing loads evenly across the entire assembly. This ensures that the foundation can withstand the dynamic forces of the marine environment.
Pin Piles
The pin piles are integral components that penetrate the seabed, anchoring the jacket foundation firmly in place. Usually these piles come in diametres ranging from 1.5 to 2 metres (5’ to 6’), with thicknesses typically ranging from 40 to 80 millimetres (1”5/8 to 3”3/16); however, in earthquake prone areas, the diametres can go up to 3,5/4m (12’/13’). The pin piles provide the necessary stability to withstand the forces of waves and currents.
DAVI SOLUTIONS FOR JACKET FOUNDATIONS
ENHANCED FLEXIBILITY FOR BETTER FORCE DISTRIBUTION
One of the key advantages of Davi's MAV 3-Roll lies in its exceptional flexibility. This flexibility translates into improved force distribution during the fabrication process. With the MAV system, we can expertly handle various aspects of jacket foundation production, including the shaping of critical components like legs, nodes, braces, and transition pieces.
THE UNPARALLELED PERFORMANCES
Davi's MAV 3-Roll with Variable Axis sets standards for performance in jacket foundation fabrication. Its cutting-edge technology, combined with the expertise of our team, guarantees that every component is crafted with the utmost precision and consistency. This level of excellence ensures that the jacket foundation will not only meet but exceed industry standards. and stability to support the weight of the offshore structure.
GREATER PRECISION IN NARROW DIAMETERS
Fabricating jacket foundations often involves working with components of varying diameters, some of which can be quite narrow. Davi's MAV 3-Roll excels in these scenarios, providing superior precision in shaping and forming even the smallest elements of the foundation structure. This precision ensures that the jacket foundation components meet the exact specifications required for stability and structural integrity.
With this solution, we offer our clients the assurance of superior quality, precision, and adaptability, ensuring the success and reliability of offshore installations for years to come.
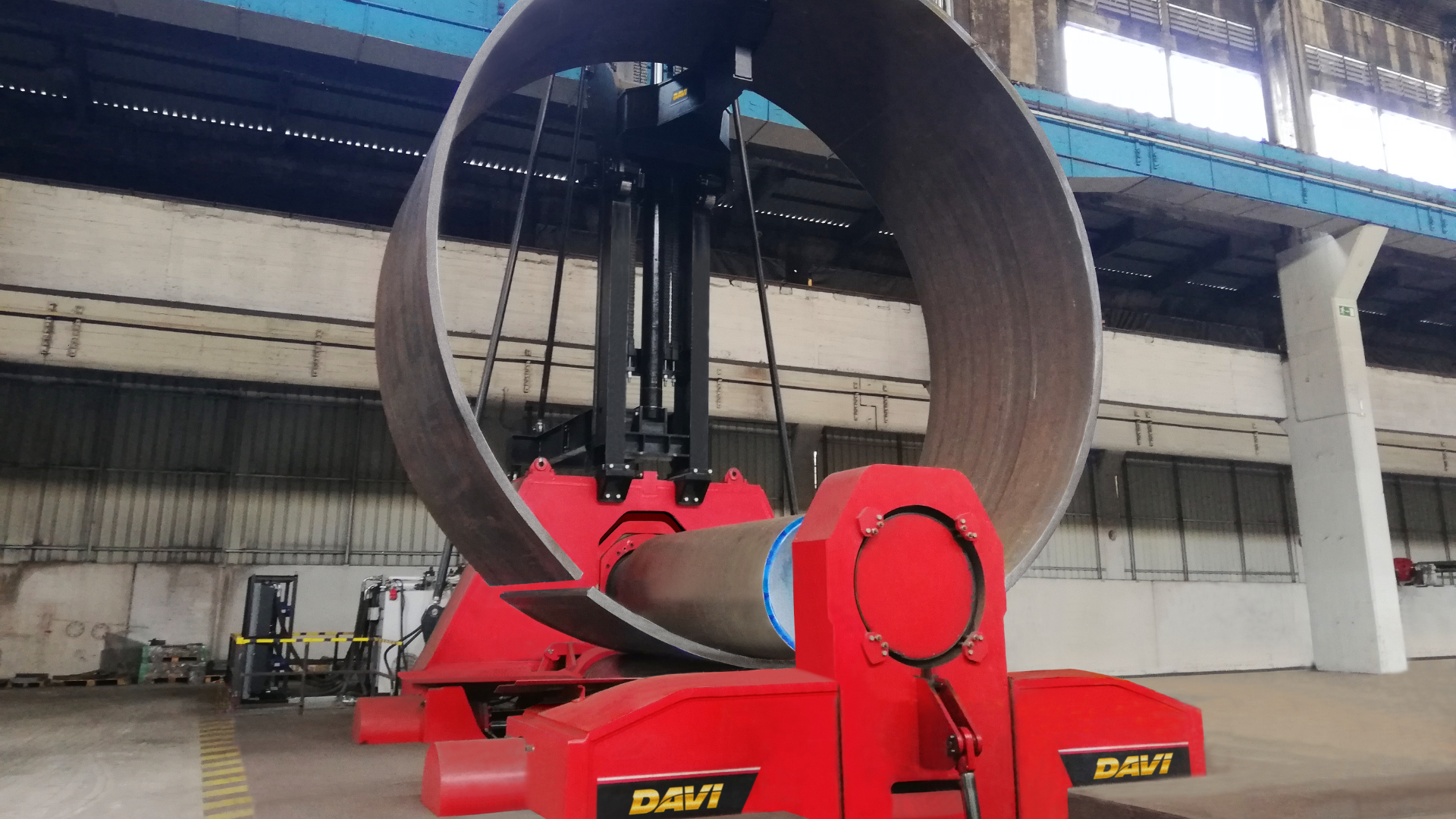
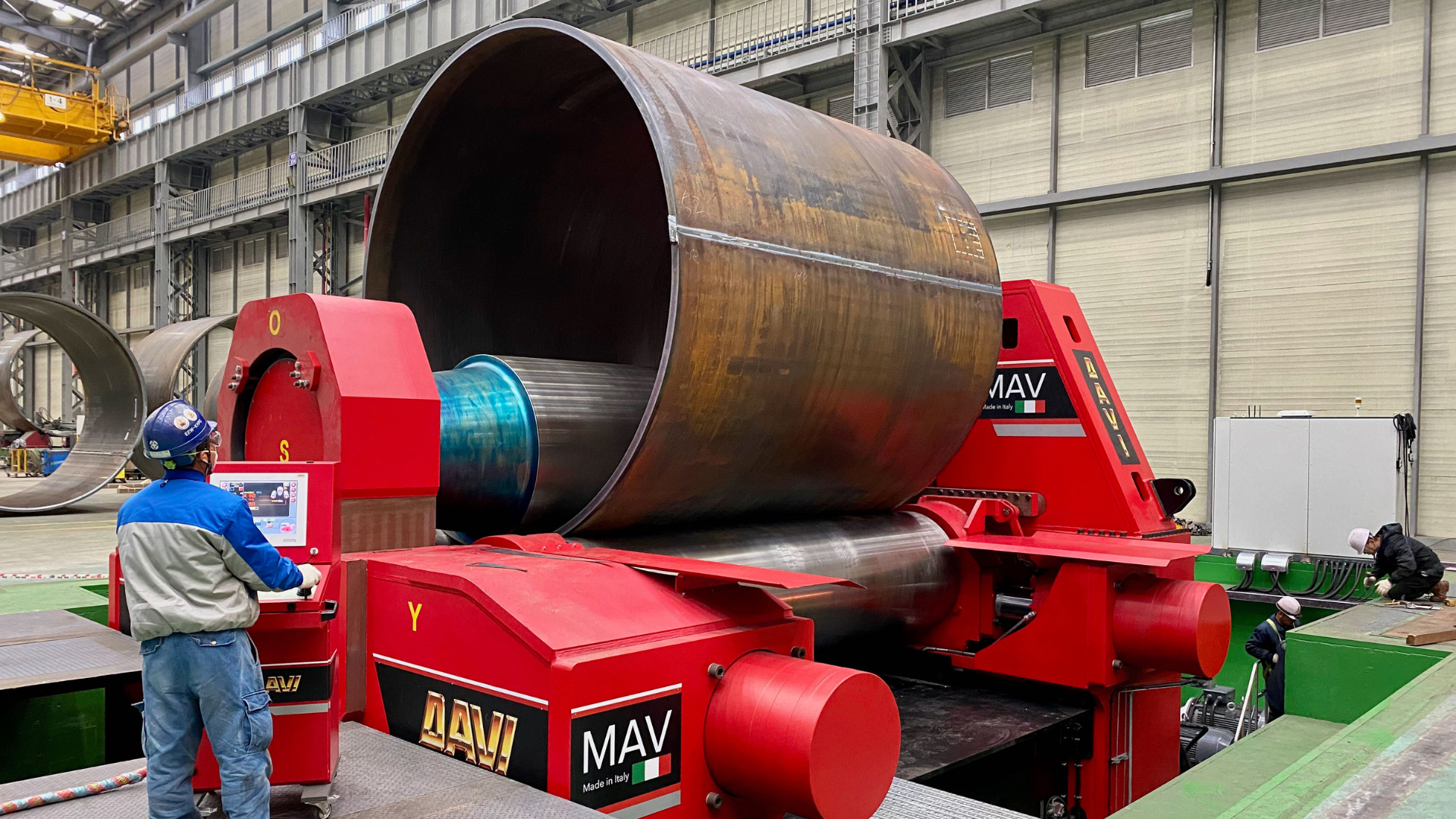
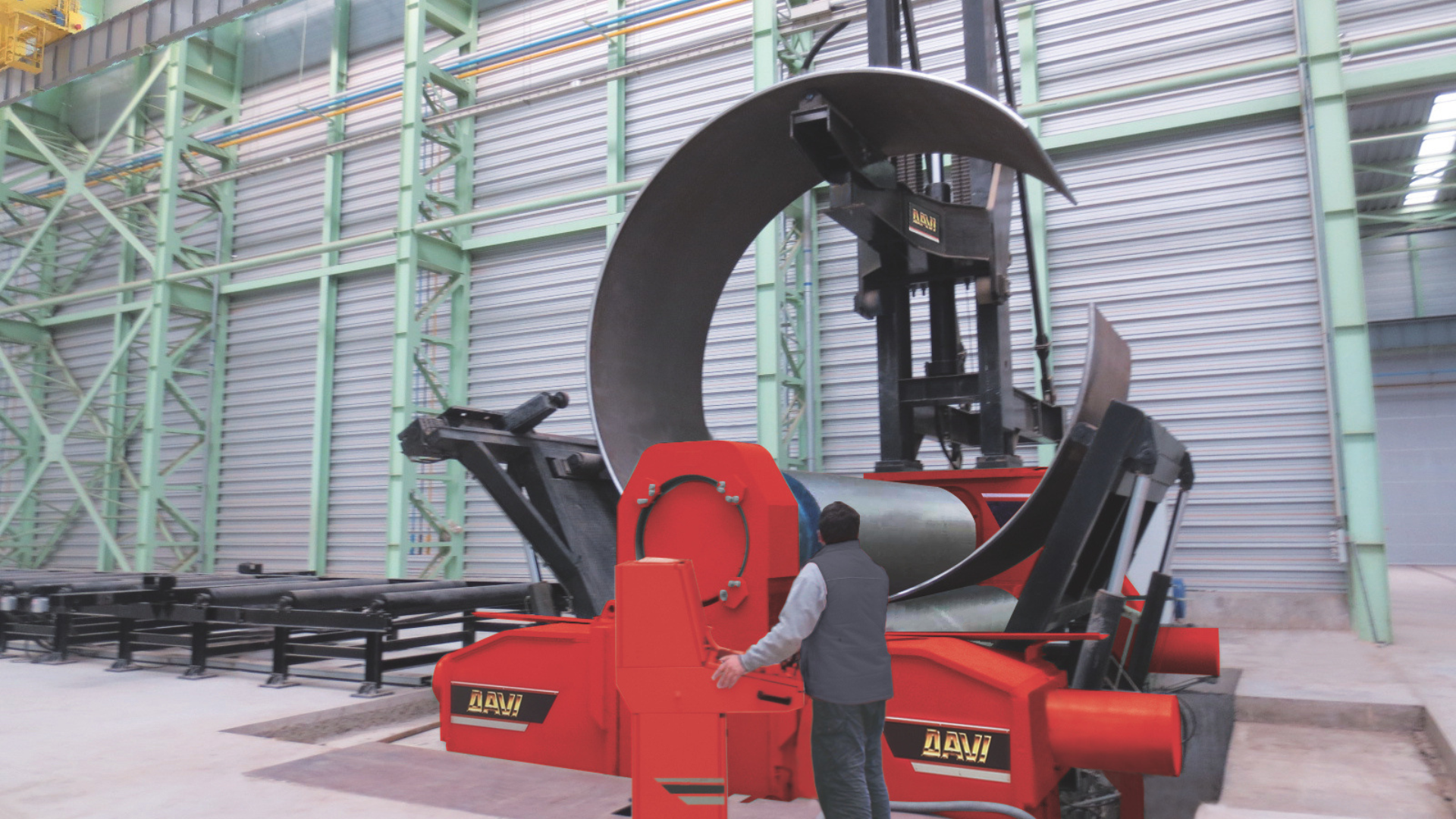
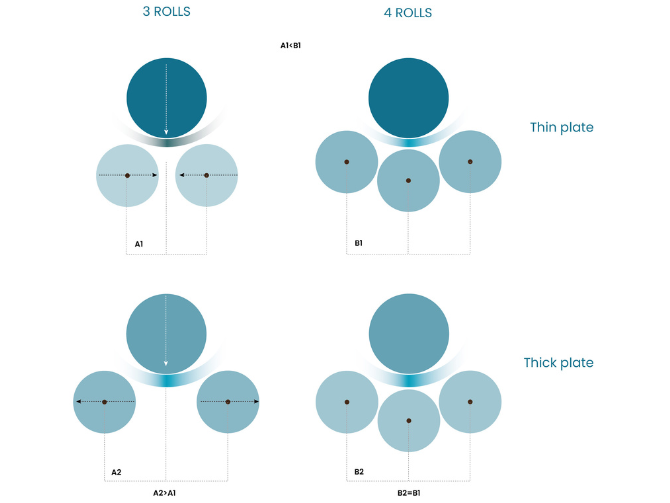
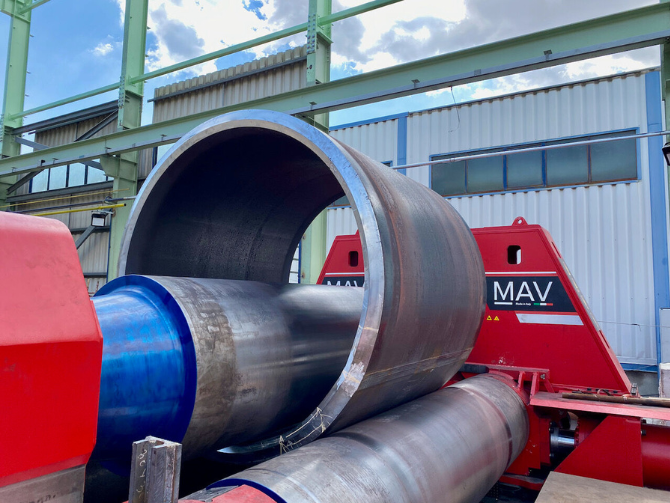
RE-ROLLING
Re-rolling can be done with both the 3-roll (preferred solution) or the 4-roll. The 3-roll MAV is more flexible as it can adapt its geometry based on the thickness of the sheet to be calibrated. It can also tilt all three rolls, allowing for precise alignment of the point of tangency between the rolls and the shell along the generatrices of the cone. The re-rolling process is particularly used for foundations.
Other products
MEDIA
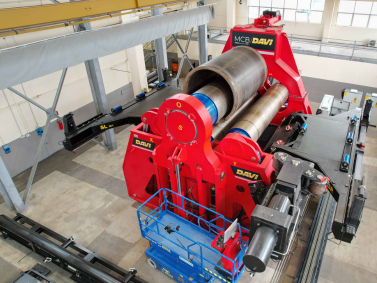
In 2024, Davi solidified its leadership in the wind energy sector by delivering 30 complete rolling solution lines worldwide. These tailored system...
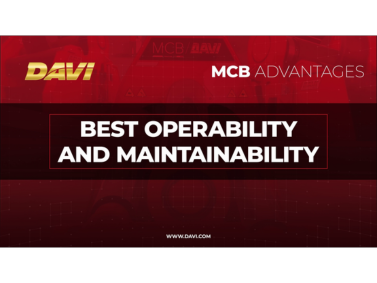
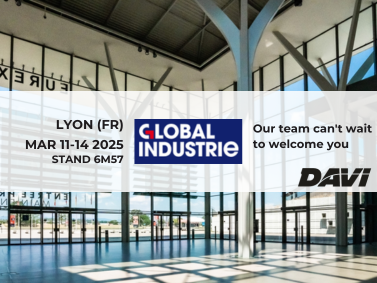
https://www.global-industrie.com/en